Lean Operations Assessment
Lean Operations Assessment
What is a Lean Operations Assessment?
Optimize your operations key resources: Evaluate and analyzes your organization's operational processes to include People, Process, Systems, Equipment, Layout, Facility.
CapRock will Identify areas for improvement and recommend solutions for increased efficiency and effectiveness.
CapRock brings an outside perspective and provides an assessment through a different set of eyes, an unbiased viewpoint that is based on facts and the learning from best practices.
20-35% Sustainable and realistic performance and efficiency gains can be obtained leveraging Lean Six Sigma Methods and the DMAIC Model.
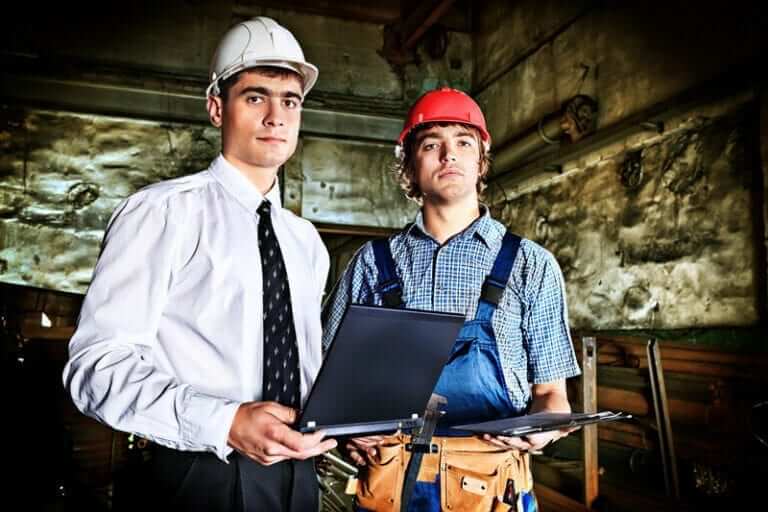
Identify and agree upon the process scope, stakeholders input; understand customer needs/requirements.
Identify key measures, sources of performance challenges, gaps, and identify ways to remove variation in performance
Improvement roadmap, streamline workflow to improve efficiency and effectiveness
Sustain performance through measurements and monitoring key indicators and results measures
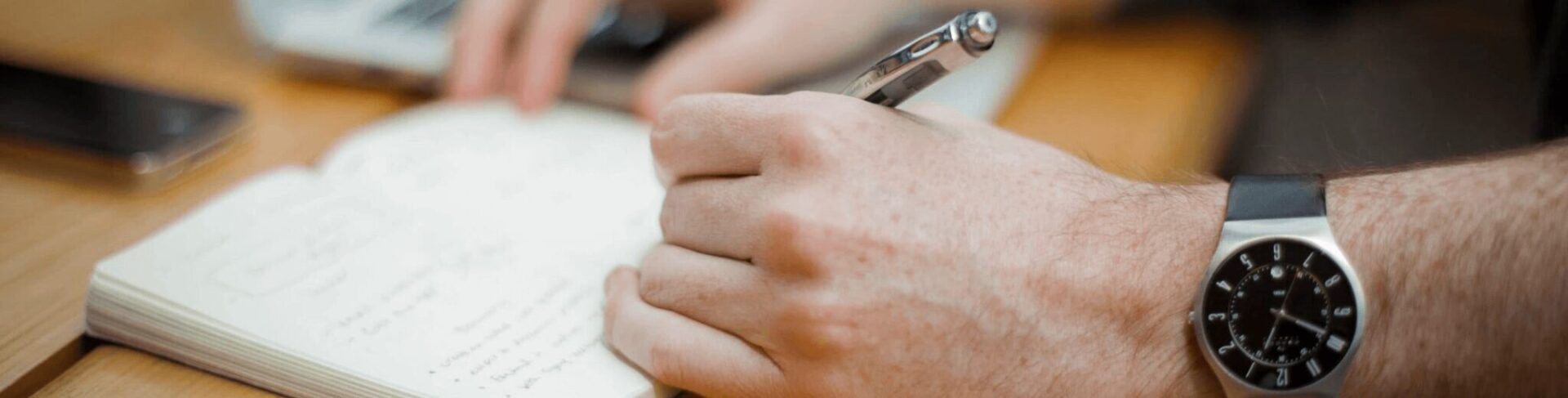
How This Helps…
CapRock operational assessment provides a check-up for your business, workflow, resources, systems, equipment, information and data flows.
Data and analytics for immediate decision-making
Improving the overall health of your company and achieving sustainable and realistic performance and efficiency gains in the 20-35% is realistic
A CapRock assessment provide short- and long-term improvement plans.
Understand, Evaluate & Improve:
- Roadblocks and Bottlenecks to Unlocking Operational Performance, Capacity and Quality
- Understand the Time Spent on Key Activities and Identify Improvements to Increase Labor Utilization and Efficiency
- Value & Non-Value-Added Tasks
- Work Delays, Idle time, System Delays, Etc.
- Identify how much labor is truly needed and when to schedule the labor and support
- Balance Cost/Revenue and Performance Objectives
- Balanced Score Card (Business and Operations Performance Indicators)
- Information and Material Flows
- Resource & System Gaps
- Workflow & Layout Opportunities
- Practices and Procedures Analysis: Documentation vs. Tribal Knowledge
- Training Gaps, Plans and Recommendations
What does a Lean Operations Assessment look like and how do we move forward?
Study Plan
We will meet you and understand your business needs and goals.
We collaborate with you, develop an assessment plan, and gain your agreement to perform the study and assessment.
Perform Study
CapRock will engage your team in a very collaborative way (as appropriate with your input), perform direct observations, collect input and data collection.
Our Project Engineer Team will study your operations, collecting data, insights, measuring work tasks and processes in a very seamless approach that will not impact on the work, your team or your customers.
Reporting and Improvement Roadmap
We will analyze the assessment study information, team input and data collected. CapRock will produce a thorough report with actionable improvement recommendations and ROI plan.
CapRock will provide an Improvement recommendations roadmap that can be implemented immediately (low hanging fruit), other improvements that may take weeks or in some cases months.
- The report will detail opportunities and recommendations to help your team perform the work in a more efficient way and the best supports your customers and your business.
- Identify Key enablers and measurements to grow, scale and support your customers and business objectives.
- Typical results of a study identify 20-35% improvement in efficiency and labor cost.
Lean Operations Assessment: Discovering Discrepancies!
US Retail Services Stores with over 20,000 locations in the US:
The CapRock Team has performed operational studies in our retail stores across the country. CapRock remains the vendor of choice for performing in-store studies.
The CapRock Project provided us real-world operational and workflow data, executing specific operational and customer facing tasks and routines. The results provided the data we needed to optimize our operations and better serve our customers.
We found the entire CapRock experience from initial project development, data collection, to delivery of the final report to be well planned, flexible to support our additional data needs and collaborative.
The CapRock teams are a pleasure for our frontline retail employees to work with, and they are always welcomed in our stores. Their ability to connect and partner with our employees, while collecting detailed observational data, workflows, and insights, without being intrusive is truly valuable to our organization.
Manufactures with Facilities across the US:
We retained CapRock to perform time studies, labor and workflow analysis to identify opportunities to quantify labor and process times, eliminated wasted steps and pinpoint process and workflow improvements within the US based plant.
The CapRock team delivered on the promise and provided valuable data and recommendations to help us best utilize our staff, streamline work processes and improve operations to support our customers.
The CapRock group of professionals worked in a very collaborative way with our management team and represented workforce. The CapRock team executed the project as planned and delivered the key outputs and recommendations our team needed.
I recommend the CapRock Global Solution organization.
A QSR / Restaurant Chain with over 5000 US Stores:
We have had the distinct pleasure of working with the CapRock team over the last two plus years, after performing our due diligence on engineering consulting firms specializing in labor analysis and productivity solutions. Throughout the entire project, the CapRock team has reinforced that we chose the right company.
They bring extensive experience in a variety of industries, while also having expertise in the QSR industry. This combination was exactly what we were looking for. CapRock is a true partner, getting in and really understanding our operations and helping us to develop tools and processes to take meaningful actions to improve efficiency.
CapRock has gone above and beyond to help us identify solutions, assist as we learn how to make impactful changes and keep us on the path when we stumbled.
They have worked with us to develop dynamic tools for the ever-changing business needs of now and into the future. A true partner in every sense of the word.
Industries
To support our clients with the best possible solutions and deliver on schedule without the surprises!